Electric Vehicles to be Produced in Scio
“We need more data, let’s go launch something!” George Albercook of Rocks and Robots was talking about a reconfigured trebuchet beam. He and his colleague Katie Tilton had reinforced a PVC pipe with Kevlar thread, after a failed first attempt at the A2 Mech Shop open house Saturday afternoon.
But Albercook’s enthusiasm for the empirical applies equally well to any number of the enterprises grouped under the umbrella of A2 Mech Shop, LLC, which is housed in around 3,500 square feet of space on Parkland Plaza, just south of Jackson Road. They’ve had the keys since November 2008, and set up in January.
One example of an A2 Mech Shop enterprise is REVolution Electric Vehicles, a subsidiary of Electric Vehicle Manufacturing, which expects to begin producing electric maxi-scooters as soon as July 2009 at a not-yet-finalized Scio Township location. That location will also serve as a retail storefront, explained EVM’s chief engineer, Erik Kauppi, while the A2 Mech Shop space will continue to serve as a research and development facility.
The A2 Mech Shop can be loosely described as a co-working space with shop tools. It encompasses more than just research and development on electric scooters, but that’s where we’ll start.
Electric Scooters
At the open house on Saturday, Kauppi, along with operations director Terry Richards, showed off a fully-assembled, working version of the production vehicle that’s expected to retail for around $6,500. He invited visitors with a motorcycle endorsement on their driver’s license to take the red machine for a spin. [The Chronicle lacks such an endorsement.]
The state of Michigan considers their vehicle to be a motorcycle because of its horsepower rating, which is around 8 hp. Top speed is 55 miles per hour, with a range of around 50-60 miles on a 4-hour charge. Kauppi stressed that it’s a real-world range, not the kind of idealized estimate he says is typical of the electric vehicle industry. Their goal, he said, was not to repeat the overpromise, underdeliver pattern the electric vehicle industry had seen to date.
Another pattern they’ve not repeated is what Kauppi describes as the typical electric vehicle development scheme: Invest millions of dollars in research and development to design a perfect vehicle from scratch, then go over budget and miss deadlines, never bringing a vehicle to market. Kauppi says their strategy is actually to bring a vehicle to market, then expand and revise their products in response to market feedback.
Richards said they recognize that the scooter market is a niche – it doesn’t replace four-wheels and a roof – but that within that niche they’d like to be the leading manufacturer in the U.S. They’ll be hiring locally, and there was at least one open house attendee we overheard pitching his services as an assembler of these electric scooters. Response: Send us your resumé. Assembly isn’t just bolting together a bunch of parts – some aspects involve welding and some knowledge of electronic assembly.
So how have three guys – John Harding serves as president of EVM – managed to produce their first electric vehicle with prospects of beginning assembly for the marketplace about three months from now?
A large part of that answer has to do with their strategy of using as many off-the-shelf components as possible. They’re sourcing the chassis from a motorcycle manufacturer, with the batteries plus chargers coming from a Chinese company, Thundersky. They’re also sourcing the motor and one of the two controllers that are a part of the machine. A second controller has been designed and will be assembled by EVM. Kauppi brings engineering experience from Corsa Instruments, which he co-founded in 1991. Richards brings years as a technician for Chrysler’s electric vehicle projects.
Another part of the answer is that it’s not just three guys. A theme repeated over and over at the open house in talking with different tenants was that there’s a spirit of collaboration and cooperation among the members of A2 Mech Shop – most of whom don’t work for EVM – that makes the work not just fun, but more efficient. Having heard tell more than once of the collaborative nature of the work, The Chronicle asked Terry Richards for a concrete example.
In response, Richards picked up a jig that he had fabricated for ensuring that the rear suspension was installed at the exact same distance on both sides of the bike. One end of the jig had two wrench heads welded to the square steel stock. Why two? Because Dale Grover, who’s also a member of A2 Mech Shop, had pointed out that instead of making two different jigs – one per measurement – both measurements could be enforced with the same jig, if it were made double-ended. Kauppi allowed that this was not some kind of “breakthrough idea,” but that the accumulation of helpful suggestions like this made the work easier and more enjoyable. “We’re clearly doing it wrong,” he quipped, “you’re not supposed to have fun at work.”
Etching, Milling, and Timekeeping
In addition to handing out suggestions to the electric vehicle guys on their manufacturing jigs, Dale Grover spends part of his time etching metal. At Saturday’s open house, Grover was showing kids how a large pattern could be reduced to a much smaller version through a linkage. One of those kids was Steven Martin, great-nephew of Bob Stack.
Stack has space in the rear of the building for a computer-driven milling machine, which he uses to create lithophanes (among other things). Stack explained that his mill was, while we were chatting, creating an image using a 1/32-inch bit doing .007-inch step-overs – a measure of the resolution of the milling. For this “raster pass,” the distance between horizontal passes across the material was .007 inches. An earlier step had involved the roughing out of the basic shape using a larger bit and a “vector pass” – where the bit traverses the material in a less grid-like fashion.
Stack starts the lithophane process with a high-quality photograph, converts it to a grayscale image, and from there it gets converted to a height map based on the intensity of the gray at any given point in the image. It’s the height map that the mill carves into the material – which in Stack’s case is Corian®, somewhat more durable than traditional porcelain.
Under ordinary light, the resulting image shown on a lithophane is recognizable as a basic shape. But when backlit, the fine detail in the image emerges. It’s a photographic challenge to capture the essence of a back-lit lithophane – one that The Chronicle did not meet. The Wikipedia article on lithophanes provides images showing the striking contrast.
Stack said that the lithophanes were more like a hobby at this point than a commercial enterprise. His thoughts are turning that direction, though. At the A2 Mech Shop open house he was wondering how much someone might be willing to spend for a lithophane of a favorite photograph. At the open house, Stack had his lithophanes displayed using “helping hands” (alligator clips mounted on a stand) – a display solution that would work for the owner of the image as well. Stack attributed the idea to Peter Jensen, another member of A2 Mech Shop, who builds clocks out of nixie tubes.
Stack was excited about the prospect that Jensen would acquire a larger, beefier mill and bring it to A2 Mech Shop’s space. Jensen moved into the building just last week – even though he’s been aboard in concept since the beginning. Jensen uses his current mill for fabricating enclosures for his clocks, either out of wood or metal. The bigger mill would allow him to set up and mill 10 enclosures at a time. For now, Jensen will be fabricating the enclosures at A2 Mech Shop, but continue to assemble the clock electronics at his home shop space.
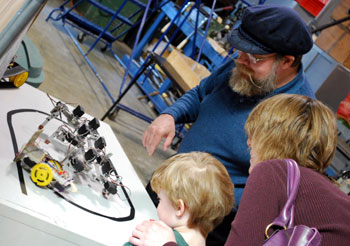
William Wardrop, whom we met as a model-builder for REVolution Electric Vehicles. He's familiar enough with other A2 Mech Shop gadgetry to demo the track-following robots for open-house attendees.
Robots Etcetera
Among the displays set up for the A2 Mech Shop open house was a robot that managed to navigate on its own around a circular path marked out with black tape. We surmised it was likely set up by George Albercook of Rocks and Robots, another member of A2 Mech Shop – but based on the number of different folks we saw introducing it to visitors, it could have been anyone. Among them was William Wardrop, who’s actually working with REVolution Electric Vehicles building models for them. Wardrop specializes in cardboard models, using a technique that involves soaking the cardboard in superglue.
At the open house, we first met Wardrop looking at an early prototype of an electric motorcycle that Terry Richards had built. The prototype featured a gas tank with a grid of holes drilled into it to help cool the battery chargers located inside. We remarked on how regular the grid was, given that it had been measured out by hand. That led Wardrop to reminisce about his grandfather, who did the pinstriping on Chrysler Imperials back in the 1930s – by hand.
Albercook and his colleague, Katie Tilton, were occupied for most of the open house undertaking design modifications to their trebuchet. The first attempt, which we missed, led quickly to an attempt to reinforce the small PVC pipe that served as the main beam in the catapult-like device. The attempt at reinforcement did not succeed, either. The third design iteration involved increasing the caliber of the PVC pipe.
The third design iteration achieved more success than the first two attempts, although success came only incrementally. After the second attempt, one onlooker declared, “It hit the ground nearby, but with much more force this time!” There was one attempt that included a backwards trajectory, and a couple that sent the golf ball on a nearly vertical path. In the attempts we witnessed, one sent the pink ball about 40 yards in the intended direction.
The key to aiming the trebuchet is a hook that determines the release point of the projectile. If the angle is too acute, the release comes too late, slamming the ball into the ground in front of the machine. If the angle on that hook is too wide, the release comes too soon, sending the ball backwards. Because the hook was smashed into the ground with each attempt, thus altering its angle from its starting position, it was hard to make the tweaks necessary.
When The Chronicle departed the open house, Albercook and Tilton were preparing to make some modifications that would allow them to dial in the hook angles for future attempts that would be a bit more reproduceable. A couple of the nearly vertical launches had given them pause – there were lots of cars in the lot belonging to open house visitors, not to mention people’s noggins that they wanted to preserve.
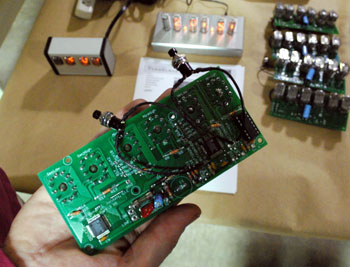
Peter Jensen holding a circuit board for a nixie tube clock, examples of which are visible in the background.
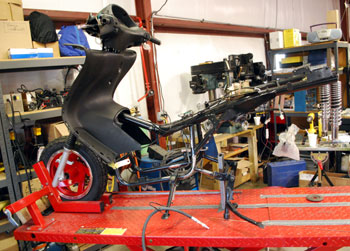
A chassis for a two-wheeled electric vehicle roughly in the same shape REVolution Electric vehicles receives them before modification.
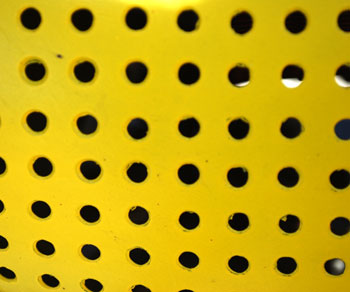
A years-old prototype of an electric motorcycle constructed by Terry Richards required drilling a grid of holes in the gas tank to help cool the charging system.
I think that I want one of these!
The A2 Mech Shop also hosts GO Tech, a monthly meetup of technology hackers/makers whose next meeting is tomorrow at 7 PM. You can find videos of previous meetings here:
Video from Vimeo of GO Tech
More photos of this weekend’s open house:
Flickr Photos of A2 Mech Shop open house
The GO in GO Tech is for Great Oak Cohousing, where A2Mech and GO Tech was incubated before they moved into their own space in the same neighborhood. Several of the principals live in one of the three cohousing communities. If you’ve heard of cohousing but think it’s just a bunch of hippies, take another look–it’s a pretty vibrant, diverse (and high-tech) place.
Check it out here: http://www.aacoho.org/