Ann Arbor MiniMaker Faire Draws 1,000+
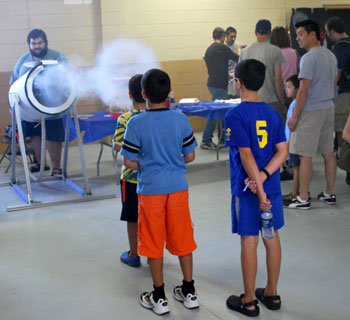
Andros Lee with his Vortex Doomsday Cannon at the Ann Arbor 2009 MiniMaker Faire. (Photo by the writer.)
Two-wheeling it southward down Ann Arbor-Saline road early Saturday afternoon, The Chronicle was passed by a car with a “Biodiesel” logo.
The sort of person who drives a car fueled with biodiesel, we figured, would be the same sort who’d be interested in robots, lasers, air cannons, and all manner of other gadgetry. So we figured a little ways down the road, that driver would be turning left into the Washtenaw Farm Council Grounds for the MiniMaker Faire.
Anyway, that’s where The Chronicle was headed – and on arrival at the parking lot, we confirmed it: Our biodiesel driver was at the MiniMaker Faire.
The “mini” in the title of the event did not refer to Andros Lee’s giant vortex cannon or Matt Switlik’s standable brush bot – more on those in a bit. Rather, it reflected the scale of the event as compared to the non-mini Maker Faires, which began in San Mateo, Calif. in 2006. That led to the second Maker Faire in Austin, which attracted 20,000 visitors in 2007. Returning to San Mateo earlier this year, Maker Faire numbers grew to an estimated 80,000 people.
As an exhibitor – even at the smaller Ann Arbor MiniMaker Faire on Saturday – standing out in a crowd of over 1,000 people can be a challenge. But Yitah Wu met that challenge by taking dead aim at folks in that crowd, including The Chronicle, with a pistol-style vortex cannon.
Vortex Cannons – Doomsday-Size It, Please!
Launched from a good 20 feet away, and guided with a laser sight, the “projectile” from Wu’s handheld cannon landed squarely on The Chronicle’s nose and unfolded across our face, giving rise to a vaguely damp and webby sensation – one that left us brushing about our face trying wipe away whatever it was.
What was it? Just a wad of air – a torroidal vortex that had been expelled from a yogurt-cup barrel by an elastic-band contracting against a diaphragm when Wu squeezed the trigger. So it worked. We were propelled towards Wu’s table to find out more about it.
Besides luring MiniMaker Faire attendees to Wu’s table, it’s useful for blowing out candles from a distance of 50 feet. He built the device mostly from items within arm’s reach – the yogurt cup for a barrel, scrap wood for the handle and cradle, a bicycle spoke as part of the trigger.
The one item he went out and bought for the project was a brass sleeve, which lines a hole in the wooden grip. The bicycle spoke slides through that hole as a part of the trigger release, and a brass-steel interface, Wu explained, offers less friction than wood-steel. And less friction means a smoother trigger release.
The smoothness of the release is important for the accuracy of a handheld vortex cannon. Wu showed us an earlier prototype that was based on a slingshot design – to fire it required drawing back the elastic with one hand and stabilizing the base with the other. The challenge of maintaining a stable base throughout the launch is the same one faced by archers – something Wu said he learned from a college classmate who was an archery enthusiast.
Next to the table where Wu was set up was the reason The Chronicle had even headed in his direction. The “whomp” from Andros Lee’s appropriately named Vortex Doomsday Cannon could be heard before it was seen.
Lee takes seriously something that Wu had explained about vortex cannons: You can manipulate the size of the barrel and the aperture for different effects. Lee’s cannon measures better than two feet in diameter. There was nothing “mini” about it. For added fun, Lee – and his fellow cannon builders Rob Spiess and Walter Fruge – had configured the cannon to blow smoke rings. Doomsday-size smoke rings.
Robots
Two different FIRST (For Inspiration and Recognition of Science and Technology) Robotics Competition teams were on hand to display their robots: Ypsilanti High School’s Alpha Omega Robotics Team 470 and Plymouth-Canton’s Team 862.
Mike Murphy, who works for the Environmental Protection Agency, is one of Team 470′s mentors.
At the MiniMaker Faire, Murphy explained to The Chronicle how the FIRST competitions work. In January of each year, “the game” for the year is introduced with the complete rules, playing field, together with a kit of parts. Teams get six weeks to build their robot.
The robot they had on hand at the MiniMaker Faire was from this past year’s competition – it was built to scoop up and deposit balls in specified locations.
Trudy Adams, who was also staffing Team 470′s table, is the Ypsilanti High School faculty advisor.
Plymouth-Canton student Ashley Saunders was at the fair demonstrating a VEX robot built by a classmate of hers, Joe Jagadics. Saunders said that people who’d stopped by during the MiniMaker Faire enjoyed waving at the robot’s on-board camera that displayed live images on a monitor.
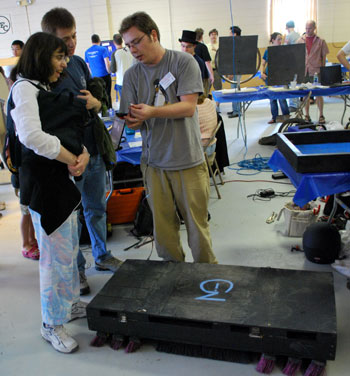
Matt Switlik shows MiniMaker Faire attendees the smaller cousins of the giant brush bot. (Photo by the writer.)
The Chronicle first noticed another kind of robot on display at the MiniMaker Faire when a guy mounted a coffee-table-sized black box. It began to shudder and vibrate, sending him on a very slow and trembly sort of journey across the floor.
It was “the world’s largest brush bot,” according to Matt Switlik. Switlik was at the event for i3 Detroit, demonstrating the super-sized version of a brush bot, which are typically made from cell-phone vibrators and toothbrush heads. In addition to the giant brush bot, i3 Detroit had a table-top arena where conventionally sized brush bots were milling about.
Brush bots aside, Switlik was also excited about the prospects of soon securing some physical work space for i3 Detroit – the three I’s in the name stand for “Imagine, Innovate & Inspire.” So they’re looking to translate imagination into a real work space.
Possibly as soon as the first of November, said Switlik, they could have a work space with CNC machines, oscilloscopes, and the like. They’re two-thirds of the way to their fundraising goal for launch, and from there the rent will be paid with membership dues. The potential spaces they’re considering are all in northern Detroit, where most of the i3 Detroit members live.
Music
Towards the front doorway of the farm council grounds building where the MiniMaker Faire was held, there was an outright assault on the auditory senses due to two different devices engineered by Matt Mets. One was his Laser Harp. It’s pretty straightforward in concept – think about what a harp would be like if the strings were laser beams instead of wire.
In the base of the rectangular frame sit individual lasers aimed at photo sensors in the top. When a beam is interrupted, a signal is sent to a controller that causes the note corresponding to that “string” to be generated.
The cacophony in Met’s corner of the faire was actually a positive sign. It meant that people where trying out the harp. Some people approached it string-by-string with a musical sensibility, while others just swiped through the space in the frame to verify that, yes, this thing really works.
Mets told The Chronicle he’d had the Laser Harp at the Maker Faire in Austin. There, a professional theramin player had taken a turn at the harp and actually played it properly. What a theramin has in common with the harp is that both are played without any tactile feedback from the instrument to the musician. Mets himself says he can pick out simple tunes on his device, but nothing elaborate. No one has yet composed a musical piece specifically for the Laser Harp, but Mets sounded receptive to the idea.
Another musical device Mets had on display was the optical equivalent of an old-fashioned music box that uses protrusions in a revolving disk to pluck the teeth of a comb – each tooth tuned to a specific note. [The Chronicle owns such a device.] In Mets’ device, the protrusions on the disk correspond to magnets that are placed on a rotating wheel – hence the name Ferrous Wheel. The locations of the magnets on the wheel are picked up by a camera, sent to a computer, and translated into notes.
The Ferrous Wheel is something Mets is working on as an exhibit for a children’s museum in Pittsburgh, where he now lives. And that’s partly what drove his choice of magnets over, say, pegs that would fit into a hole. With pegs, Mets cautioned, there’d be a risk that a kid might grab hold of one and be lifted by the rotating disk.
Silk Screening
Bilal Gahlib of MODATI Clothing was at the MiniMaker Faire serving as an ambassador for not just his company, but for the technology of screen printing. Whether it was mugging for the camera behind little kids, or handing out hugs to someone in line – just because that person was smiling a lot – Gahlib was generating goodwill for his craft that went beyond the free screen-printing he was doing. Pictures are better than words, when it comes to describing Gahlib.
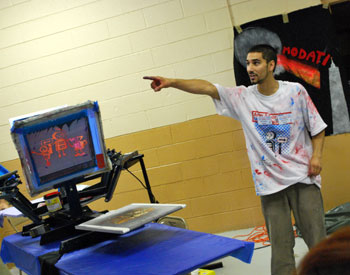
Bilal Gahlib of MODATI Clothing. Here's something Bilal Ghalib has probably never said in his life: "I'm very shy, could you please point the camera the other way?" (Photo by the writer.)
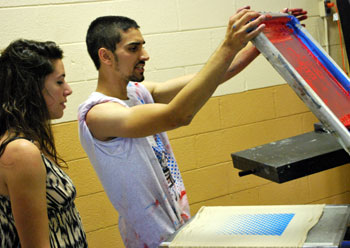
Bilal Ghalib shows Adrienne Berry the result of the first layer of color laid down by the screen printing process. (Photo by the writer.)
More Photos
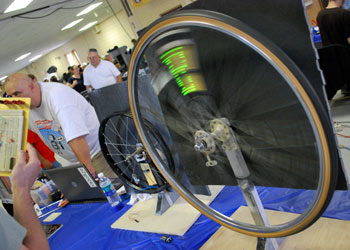
The "B" generated on the spinning bicycle wheel stands for "Bob," as in Bob Stack, who can be seen leaning on the table to the left. The letters in Bob's name were generated with a single line of LEDs that were keyed to light up in sequence as they passed a sensor. The perceived letter shapes are due to an effect called "persistence of vision" or POV. (Ed. note: corrected from "perseverance.") (Photo by the writer.)
Some photos and videos from the Ann Arbor Mini Maker Faire:
link
Congrats to Dale, Bob, Adam, Jim, and all the other a2makerfaire organizers, exhibitors, and volunteers for such a successful event! Looking forward to the full-blown Maker Faire next year in the Motor^H^H^H^H^HMaker City!
HAD A MARVELOUS TIME AT THE A2MMF! So many curious patrons and so many great minds and gadgets! Many MANY thanks to Dale and Adam for keeping in close contact with me. Definitely looking forward to the FULL-BLOWN DET-MI Makerfaire!
Cheers!
C.G. in Det.MI.
My eight-year-old son and I had a wonderful and educational time there. I appreciate how kid-friendly and acceptable the event was. Plus, I loved how knowledgeable the expediters were. It helped me remember why I like being an engineer.
Much thanks to everyone who made the event possible.
“persistence of vision”, actually
Proud of my man Andros!
Amazing time, Thanks to everyone that made this possible. We can not wait to have another. It is nice to see everyone come together and share our knowledge and talents.
CRAZY event, lots of fun. Can’t wait to start planning the next one!
Great to see you inspiring the NEXT generation of engineers, Andros… :)
Very cool. I’ve attended the Austin Maker Faire both years and have always enjoyed the exhibits. I hope Austin considers hosting a mini-Maker Faire.
:D